Incremental innovation
Driven by the belief that perfection is a vanishing point, we relentlessly explore and investigate new materials, technologies, and all methods of manufacturing. Discover how we enhance our garments, implement state of the art techniques, and explore encounters between industry and innovation in the Index.
Styles
Dyeing Techniques
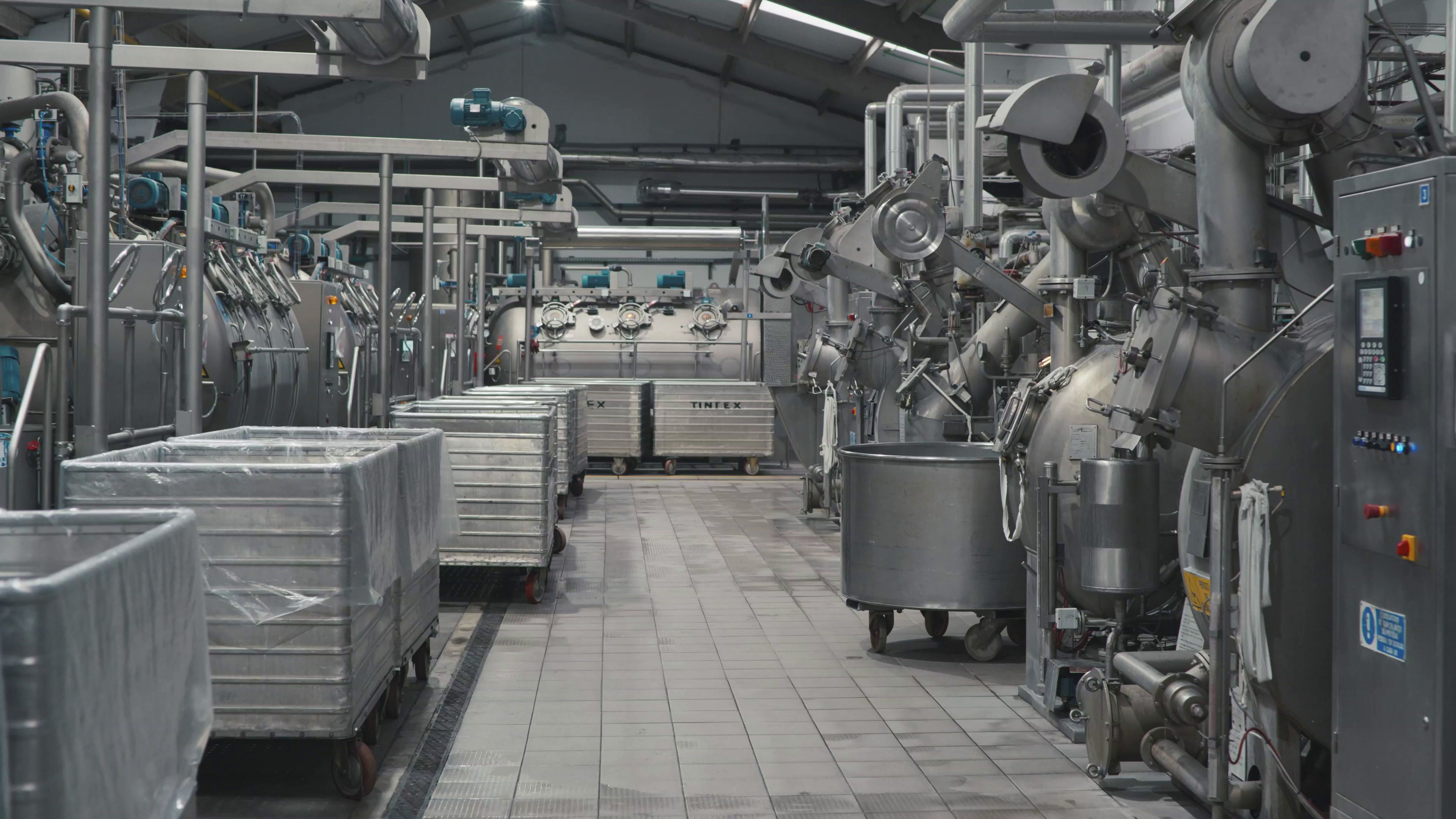
Piece Dye
Piece dyeing takes place after the knitting process, before pattern pieces are cut and sewn into finished garments.
During piece-dyeing, entire rolls of fabric are dyed at once. During this process, a continuous length of material is passed full-width through a trough of hot dye solution. The cloth then goes between padded rollers that squeeze the colour in evenly and removes any excess liquid. Generally speaking, this process results in more uniform colouration.

Garment Dye
Garment dyeing is the dyeing of finished garments in an industrial tumbler (drum).
Garment dyeing- occurs after garments have already been cut and sewn. Instead of passing entire fabric rolls through a dye bath, pre-sewn t-shirts, hoodies, sweatshirts, etc are placed in a large tumbler drum and dyed. This process can leave tightly sewn seams slightly less dyed and increases the unique character of our naturally dyed garments.
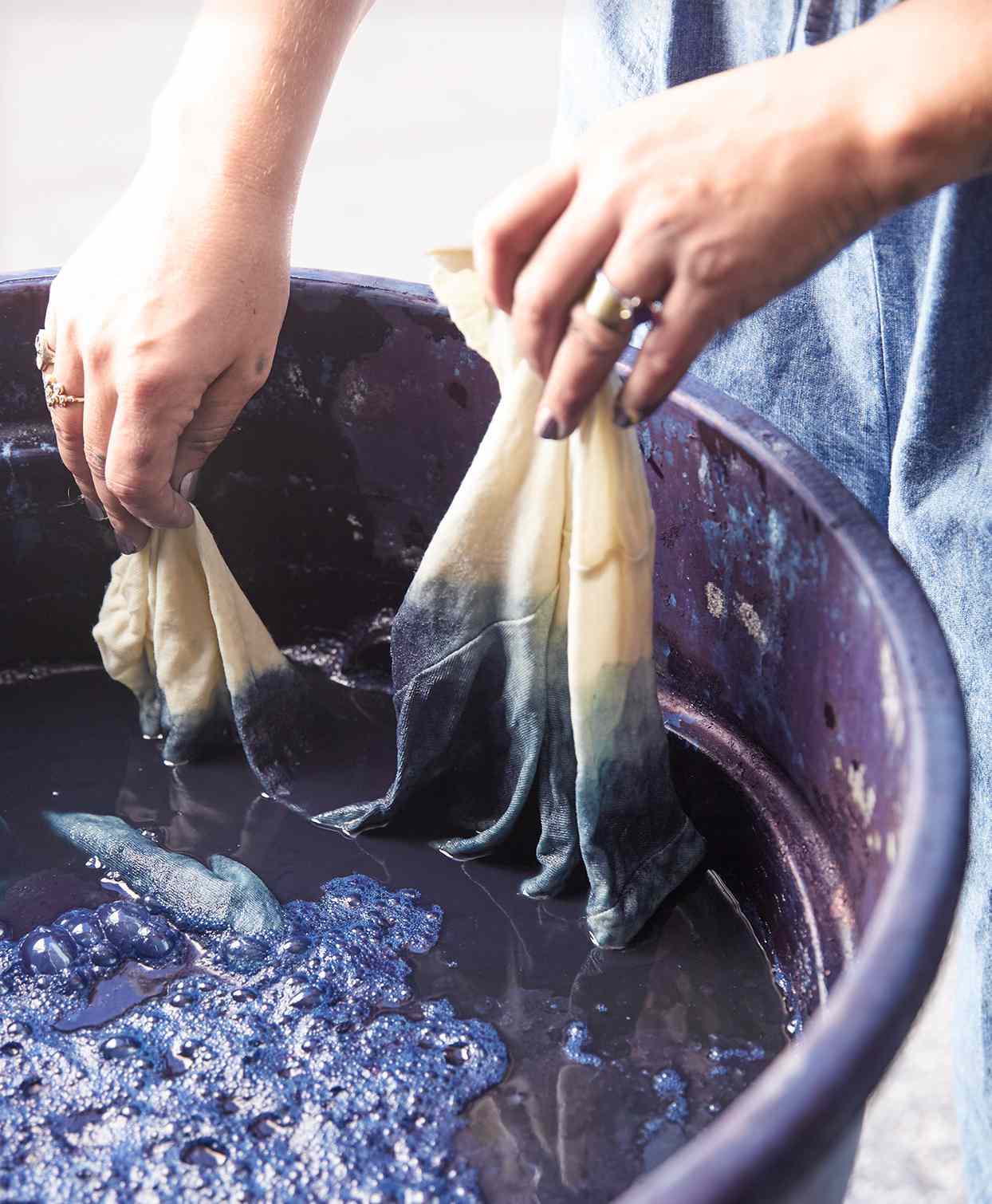
Natural (vegetable)
Dye extracted from plant sources. Our natural dyes are extracted with water during a 100% ecological practice that also offers 80% biodegradability. Even the remaining waste has its use as biofuel, fertilizer, or compost.
As natural dyeing is an irregular process, there may be small differences and shades between garments. With this type of dyeing we cannot guarantee good rubbing fastness as the dye remains on the garment’s surface. Be careful of contact with light coloured fabrics, furniture, and other fabrics. Characteristic discoloration of natural dyed garments can appear after washing and exposure to natural light.
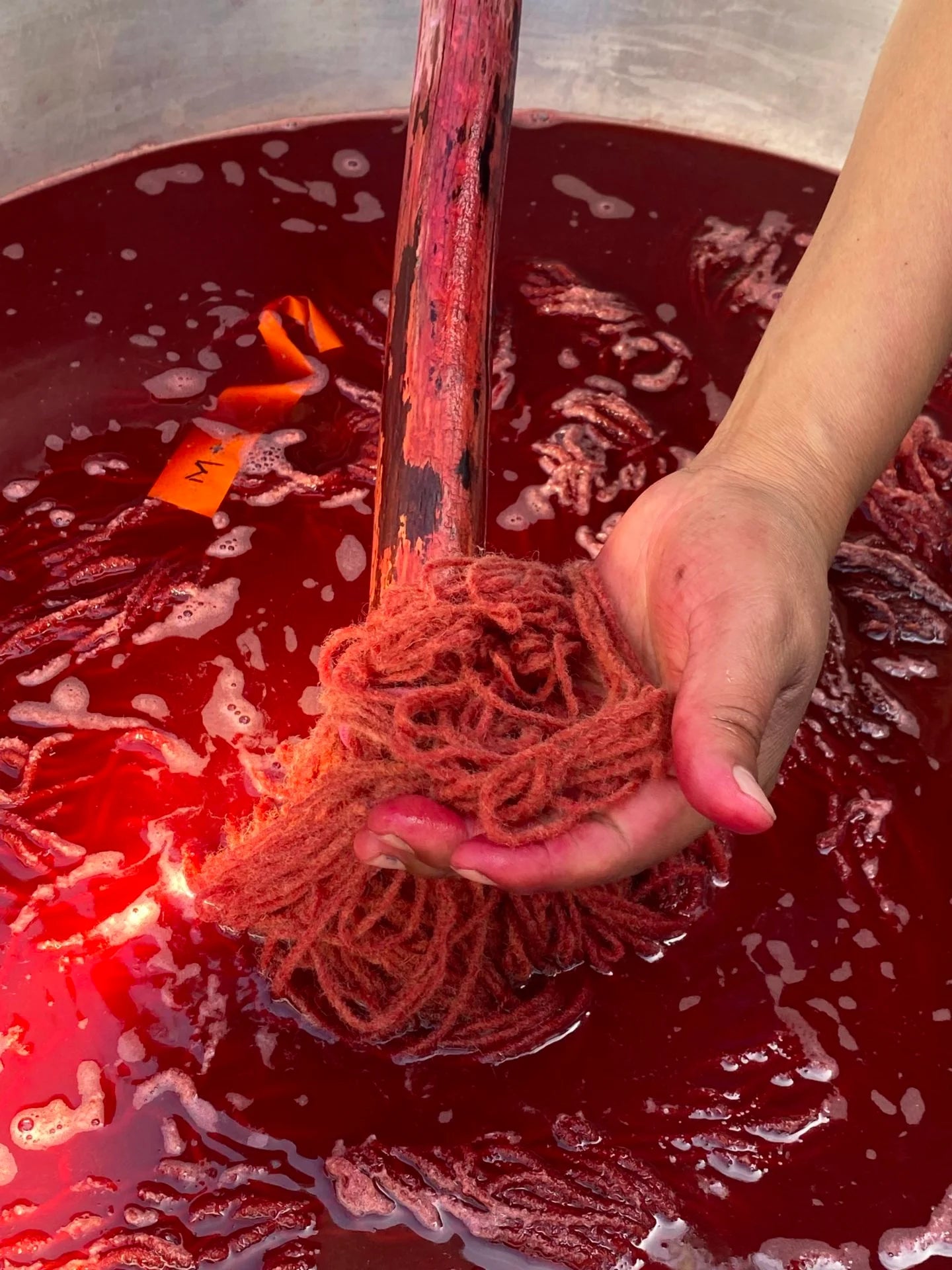
Natural (insect)
Dye extracted from insect sources. Our natural dyes are extracted with water during a 100% ecological practice that also offers 80% biodegradability. Even the remaining waste has its use as biofuel, fertilizer, or compost.
As natural dyeing is an irregular process, there may be small differences and shades between garments. With this type of dyeing we cannot guarantee good rubbing fastness as the dye remains on the garment’s surface. Be careful of contact with light coloured fabrics and furniture. Characteristic discoloration of natural dyed garments can appear after washing and exposure to natural light.
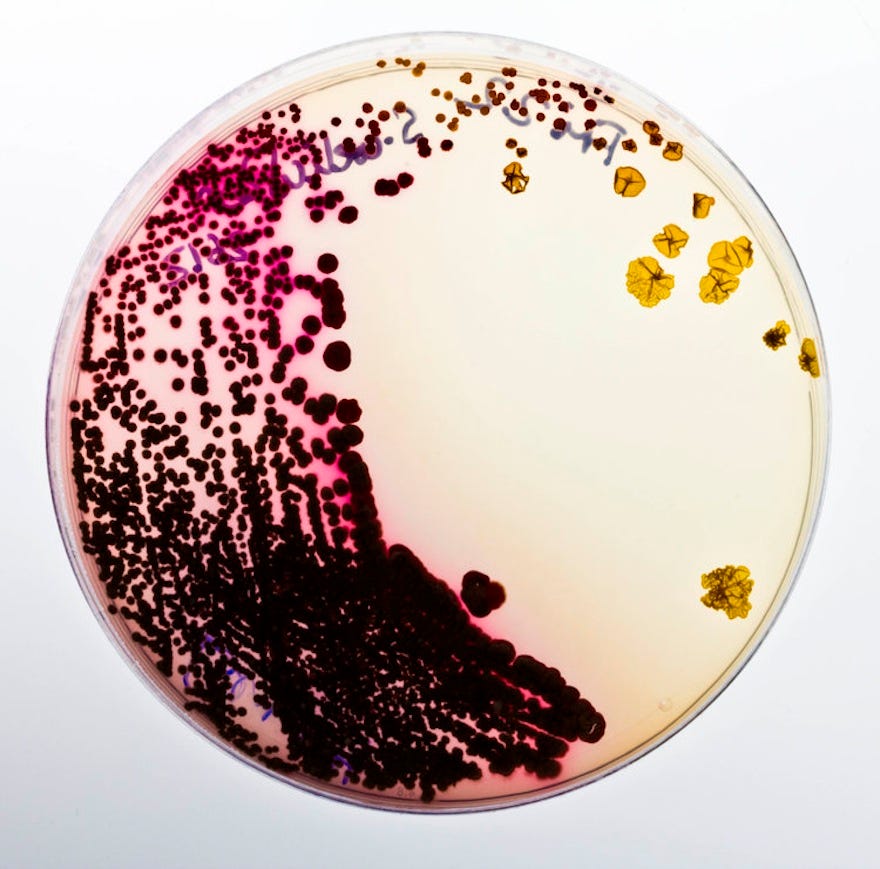
Microbial
Colorifix has developed a method of dyeing with microbes which offers a sustainable alternative to conventional dyes. Through DNA sequencing, Colorifix encodes instructions to make a pigment in a given organic compound (plant, mineral, animal, etc.). Then they translate that message into engineered microorganisms, which both grow and transfer the colour.
The microbes grow the colour, via fermentation, using by-products of the sugar production industry. The microbes infiltrate the fabric and deposit to fix the fabric with the dye. They also release metals and salts that are used in the fixing process. This way the need for mordanting agents is eliminated as the organisms harvest the chemicals. This technology allows dyeing to take place at 37 degrees on both natural and synthetic fibres. The process cuts out the use of harsh chemistry entirely and leads to huge reductions in water consumption, while meeting all key industry standards.

Reactive
Reactive dye is a class of dye that forms a covalent bond with fibre. Usually it’s used to dye cellulosic fibres such as cotton, Tencel, or flax, but wool, silk, and acetate fibres can also be dyed by this process. Reactive dyes have good fastness properties due to the covalent bonding that occurs during the procedure.
Fabric & Materials
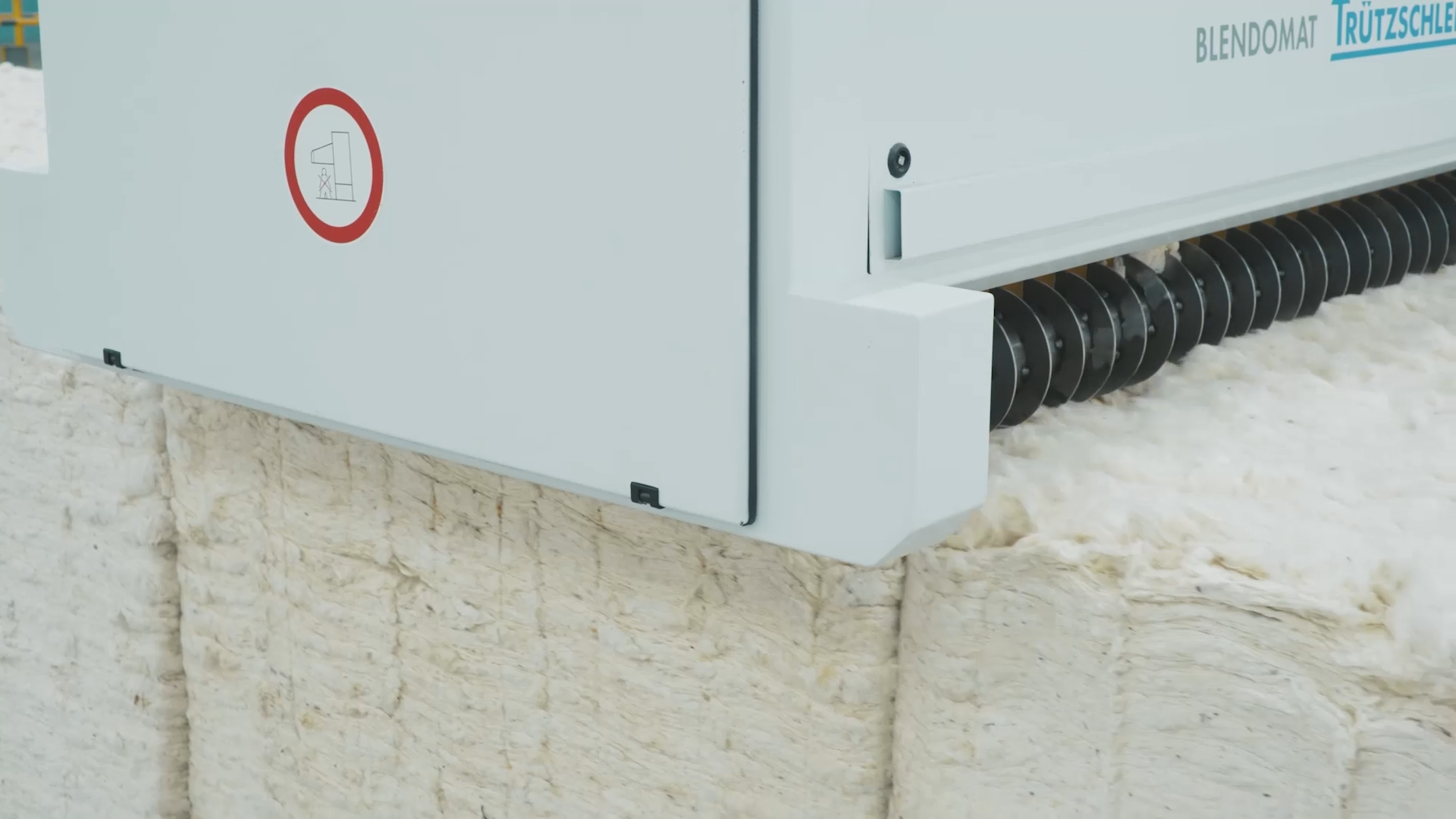
Organic Cotton
Organic cotton is generally defined as cotton that is grown from non-genetically modified plants, and without the use of any synthetic agricultural chemicals such as fertilizers or pesticides. Only the use of certified organic fertilizers and pesticides is allowed. Although organic cotton is more environmentally friendly than conventional cotton in terms of its chemical consumption, it often requires larger amounts of water and land, as it is harvested earlier to prevent later harvest loss from infestation.
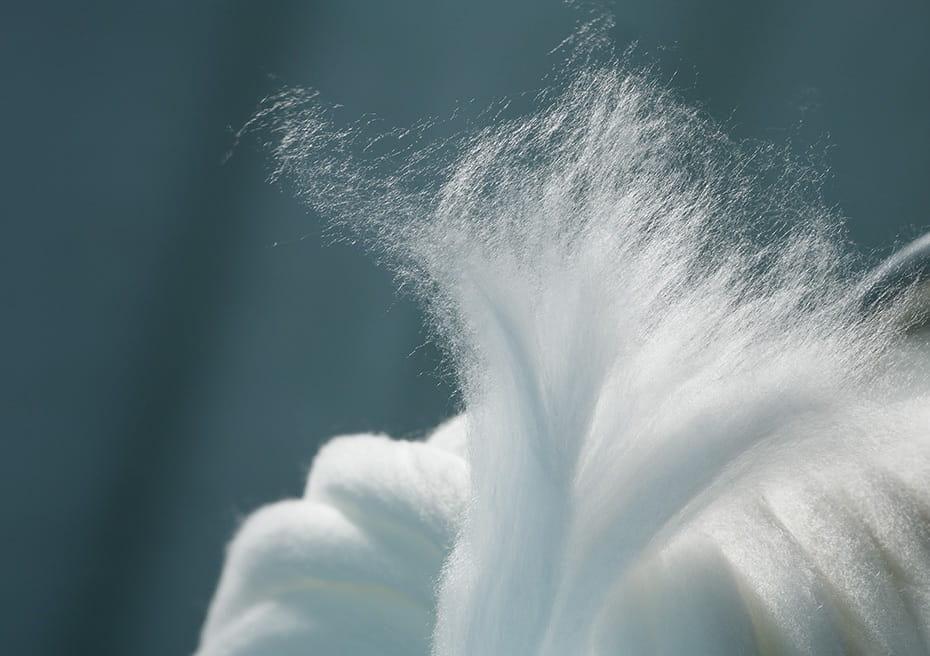
Tencel
Tencel is a sustainable fibre that is sourced from renewable raw material wood, and produced with environmentally responsible processes. It was first “discovered” by Lenzing. It requires less water than cotton production—industrially farmed cotton can use up to 20 times more water.
Tencel also requires less land; a half acre of forestland otherwise unsuitable for farming can produce enough eucalyptus trees without any pesticide or irrigation, to produce a tonne of material.
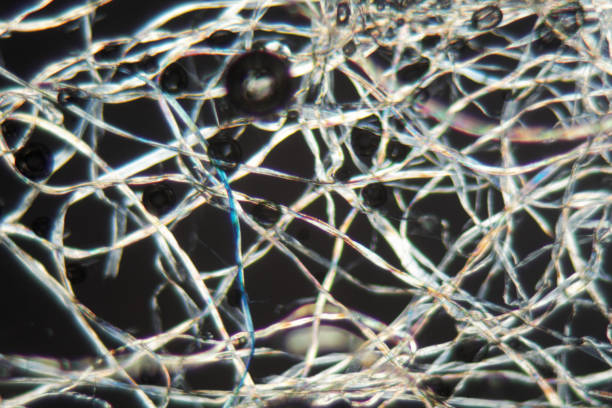
Fibres
A ‘fibre’ is defined as any material capable of being made into a fabric. It may be thought of as the smallest visible unit of textile production, or as a pliable hair-like strand that is very small in diameter compared to length. Fibres are the fundamental units or building blocks used in making textile yarns and fabrics.
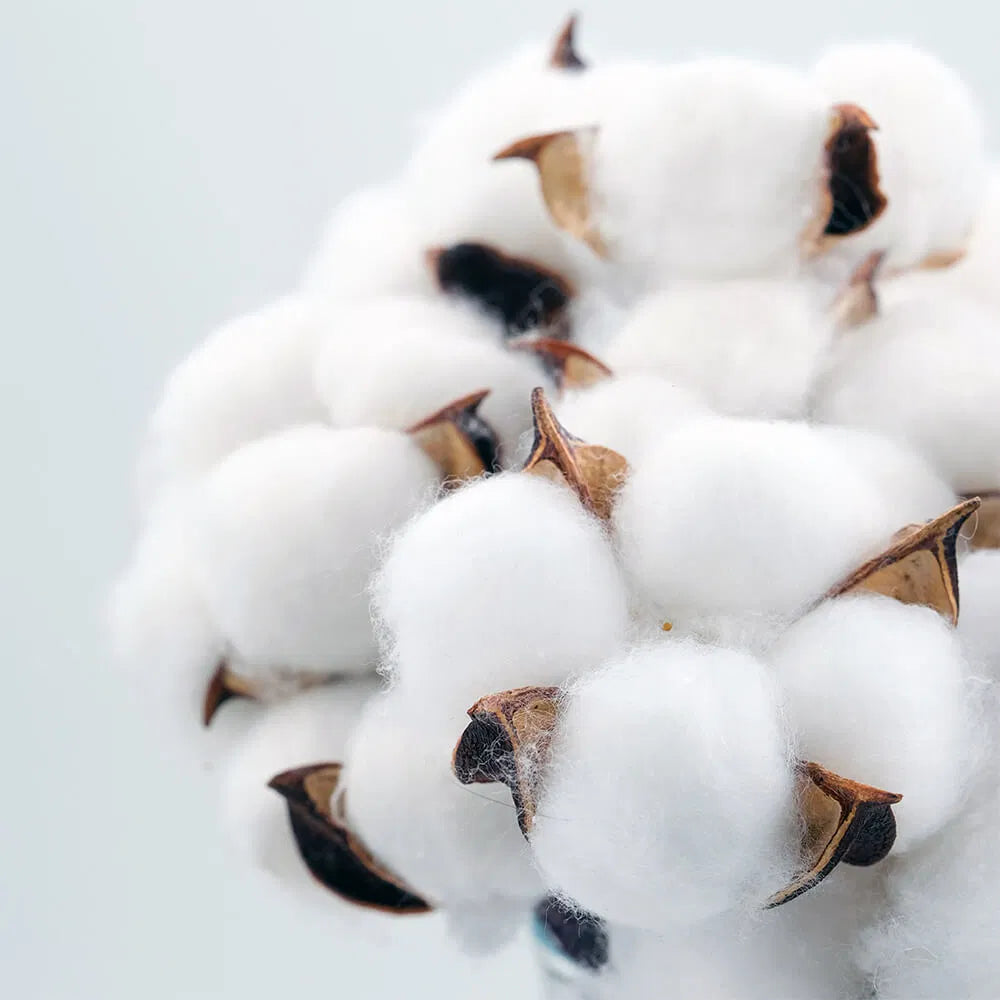
Cotton Staple
Staple fibres must be spun or twisted together to make a long, continuous strand of yarn.
Each cotton bail contains around 250,00 individual cotton fibres, or staples. The staple length varies from species to species. Generally speaking, the longer the staple length, the higher the quality. A longer fibre length results in a smoother surface with fewer exposed fibre ends. Items made with long staple cotton pill less and suffer significantly less from abrasion. Long staple cotton is much more durable, which is why certain processes, where fibres undergo strong mechanical stress, can only be pursued with long-staple cotton. Such processes include ring compact spinning and mercerization.
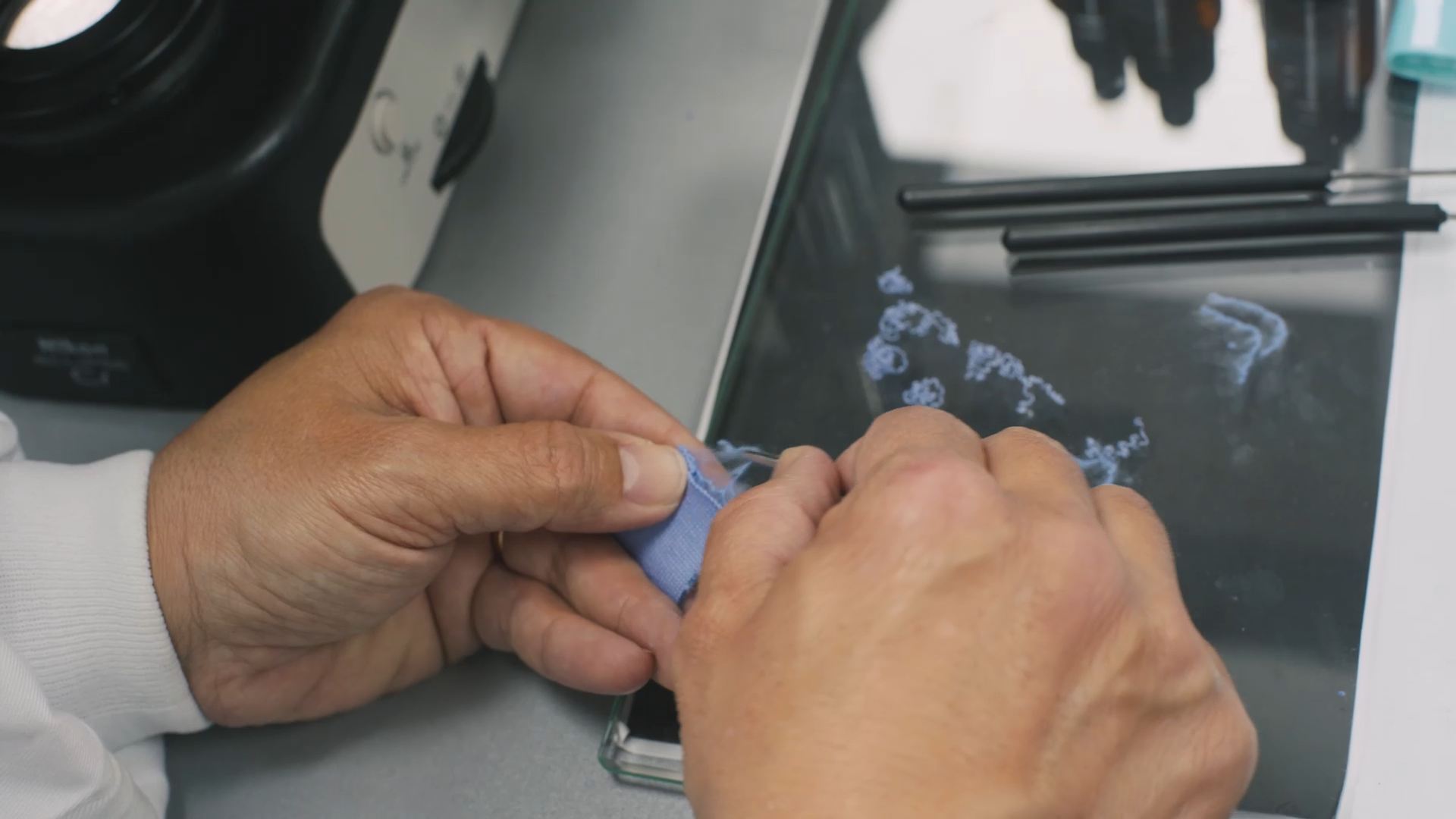
Composition
Fibre composition is an important criteria used to analyse the behaviour, properties and functional aspects of a garment. Fibre composition in garments also refers to the percentage in weight of each fibre in a fabric.
It is common practice for low quality cotton to be blended with synthetic fibres to improve yarn performance. Our 100% organic cotton reflects the high quality raw materials that go into creating a pure fibre composition.
Spinning
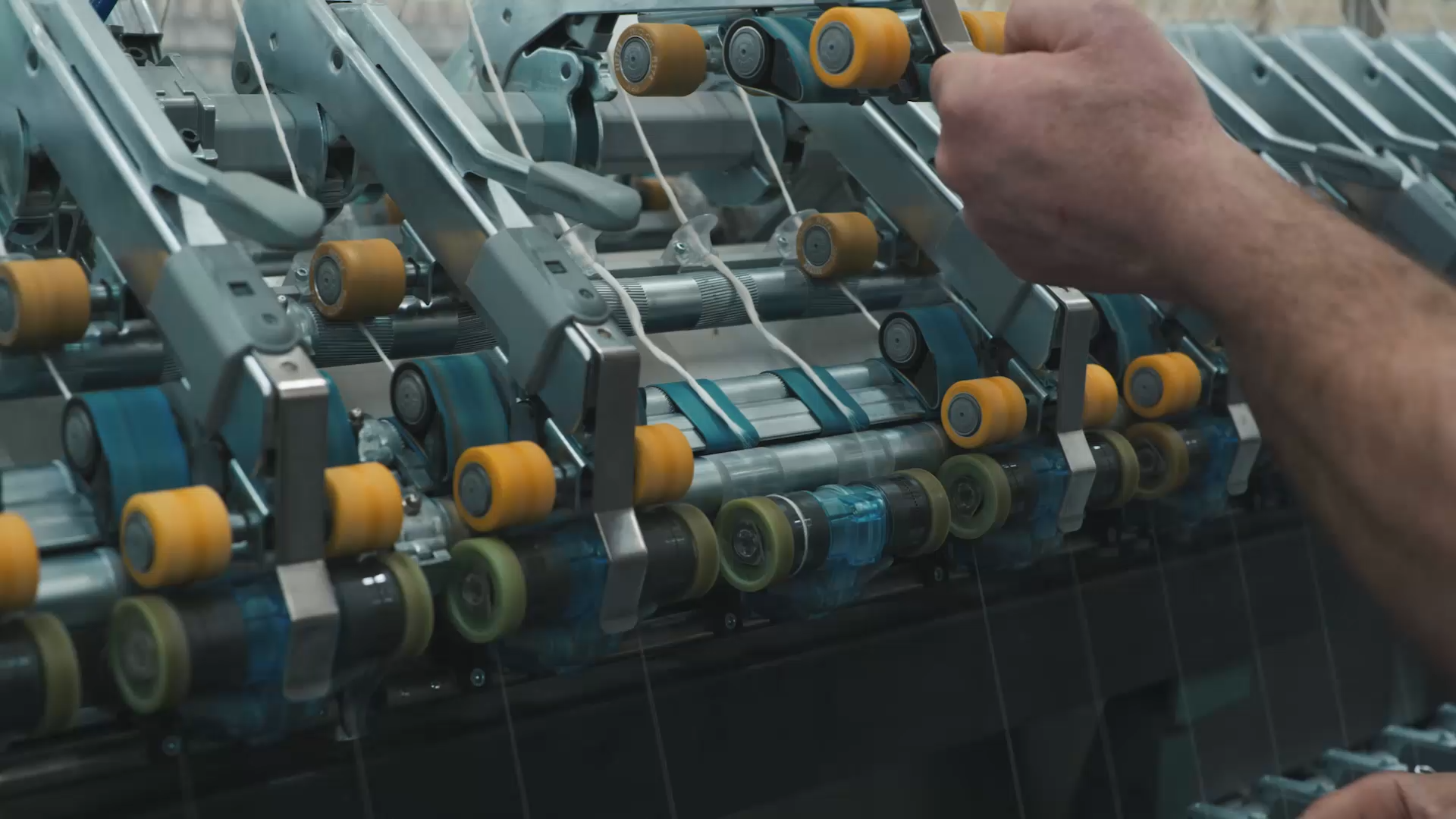
Ring Compact Spinning
The ring compact spinning technique is the best spinning technique out there. It increases the quality of the yarn by narrowing and decreasing the width of the fibre strip that leaves the stretching apparatus before being twisted into yarn. This produces a much smoother and ordered yarn with less hairiness.
The reduced torsion means that more dead matter can be eliminated during dyeing (effectively reducing the required amount of dyes and chemicals by 20% & 30% respectively). It also reduces abrasion by 30%, improves pilling performance and fabric appearance due to reduced hairiness. It also reduces shrinkage by 35–40%.
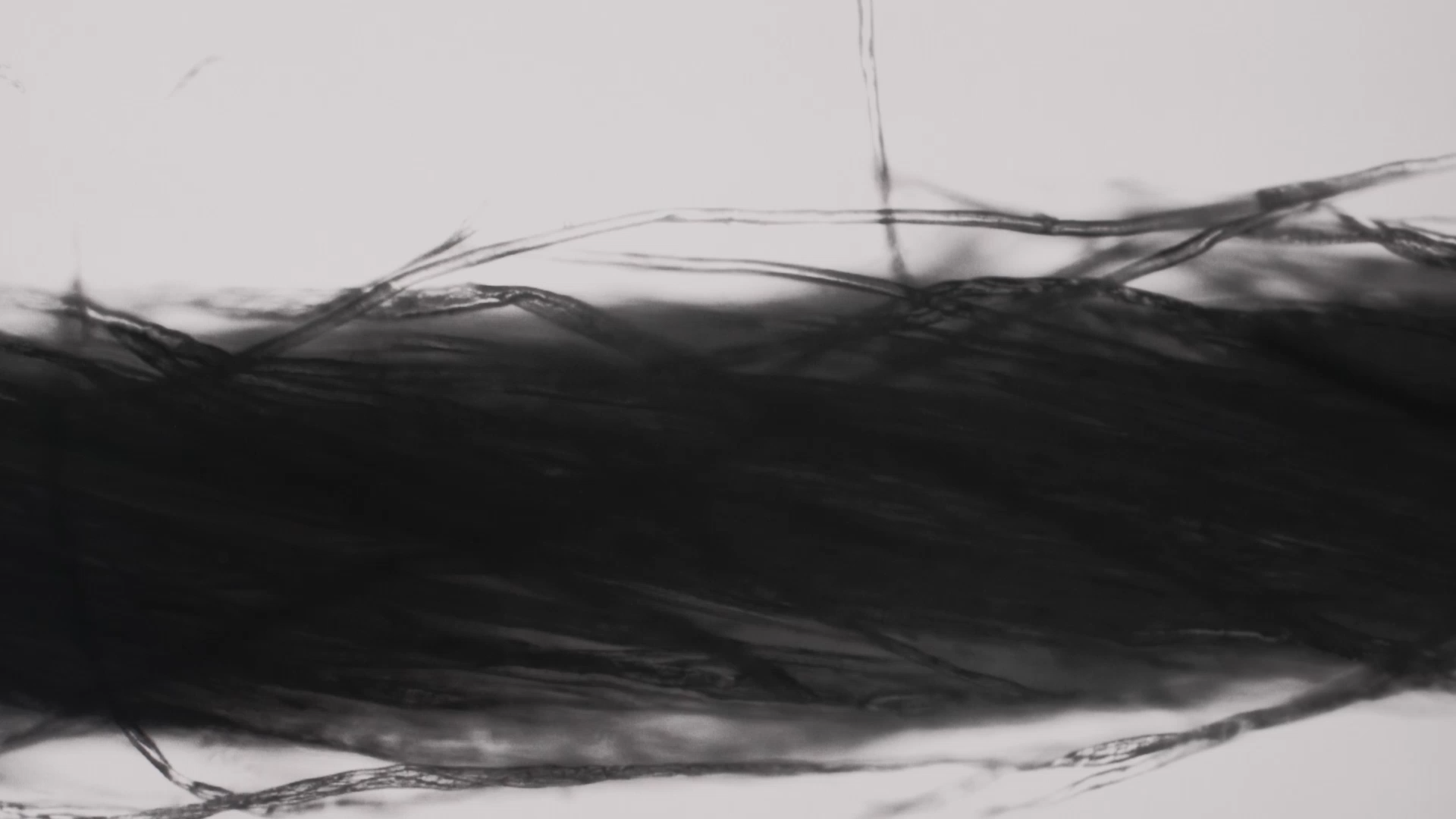
Yarn Hairiness
Yarn hairiness refers to the amount and length of fibre ends and loops that protrude from a body of yarn. Hairy yarn results in more pilling as these loosely attached ends collect at the surface to produce pill-balls. Hairy yarns also result in more muffled and less brilliant colours as light is reflected diffusely rather than directly.
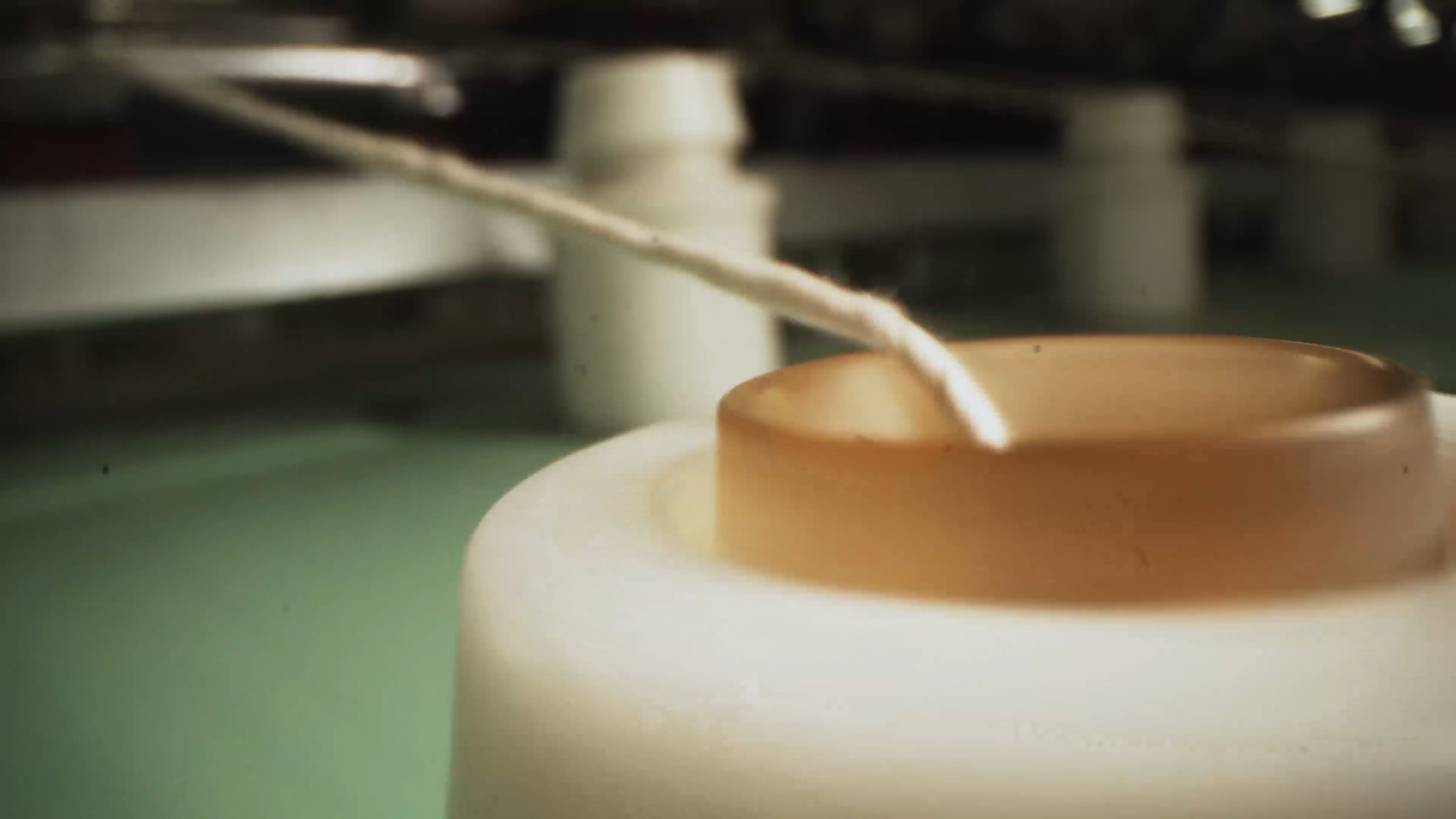
Yarn twist
The process by which fibres are arranged around the axis of yarn is called yarn twist. Through twisting, fibres are bound together and create a stronger yarn. Thisalso influences the elasticity of yarn and its propensity for abrasion. Generally speaking, the higher the twist, the stronger the yarn, until an optimum twist is reached. It can be S, left handed (regular or open hand) or Z right handed (reverse or cross hand).
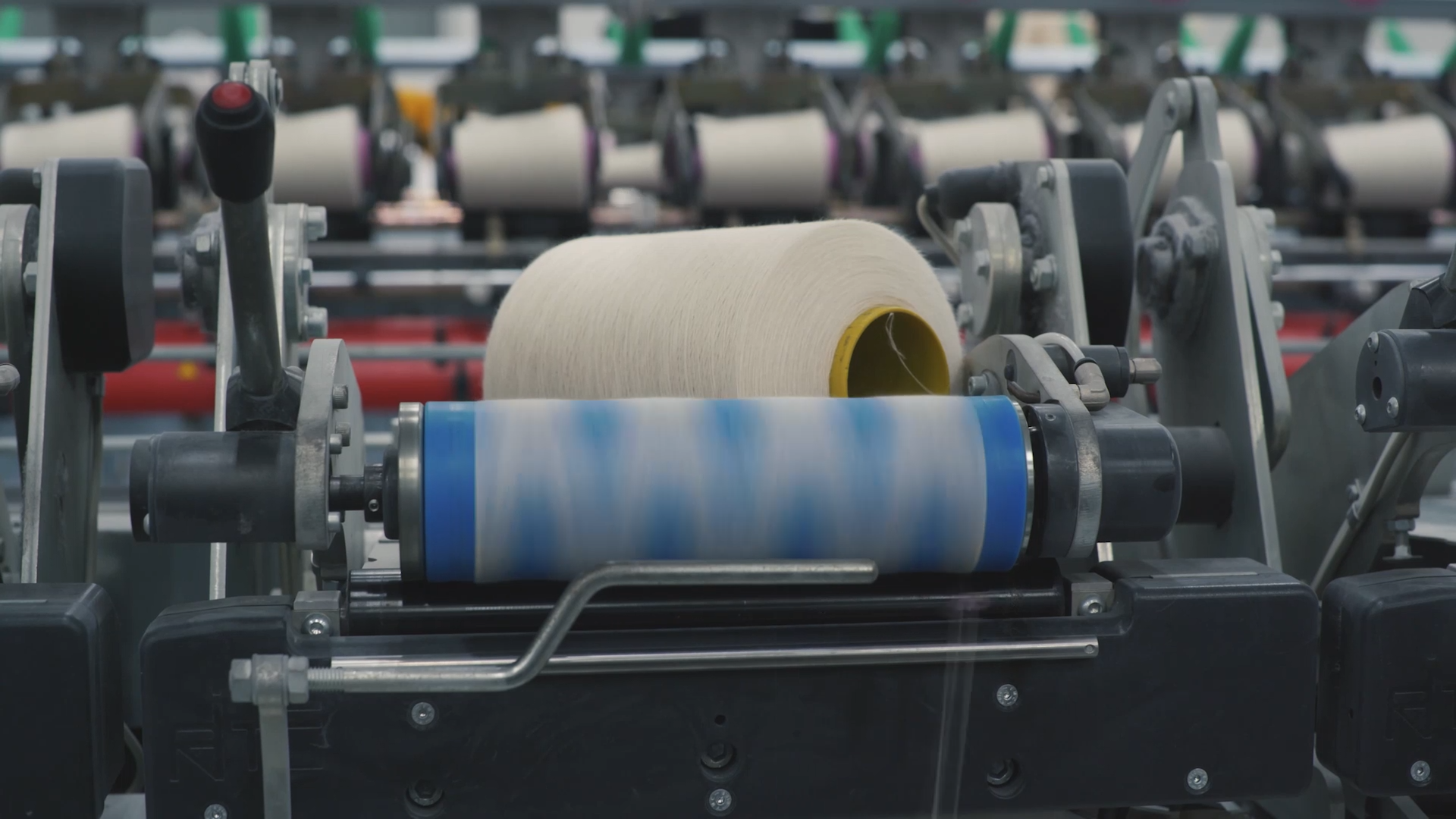
Yarn
Yarn is the result of the machine spinning process, which brings fibres together to provide different qualities and structures. Factors such as the length of the fibre, yarn count and twist direction can all contribute to the appearance and strength of a fabric.
Knitting
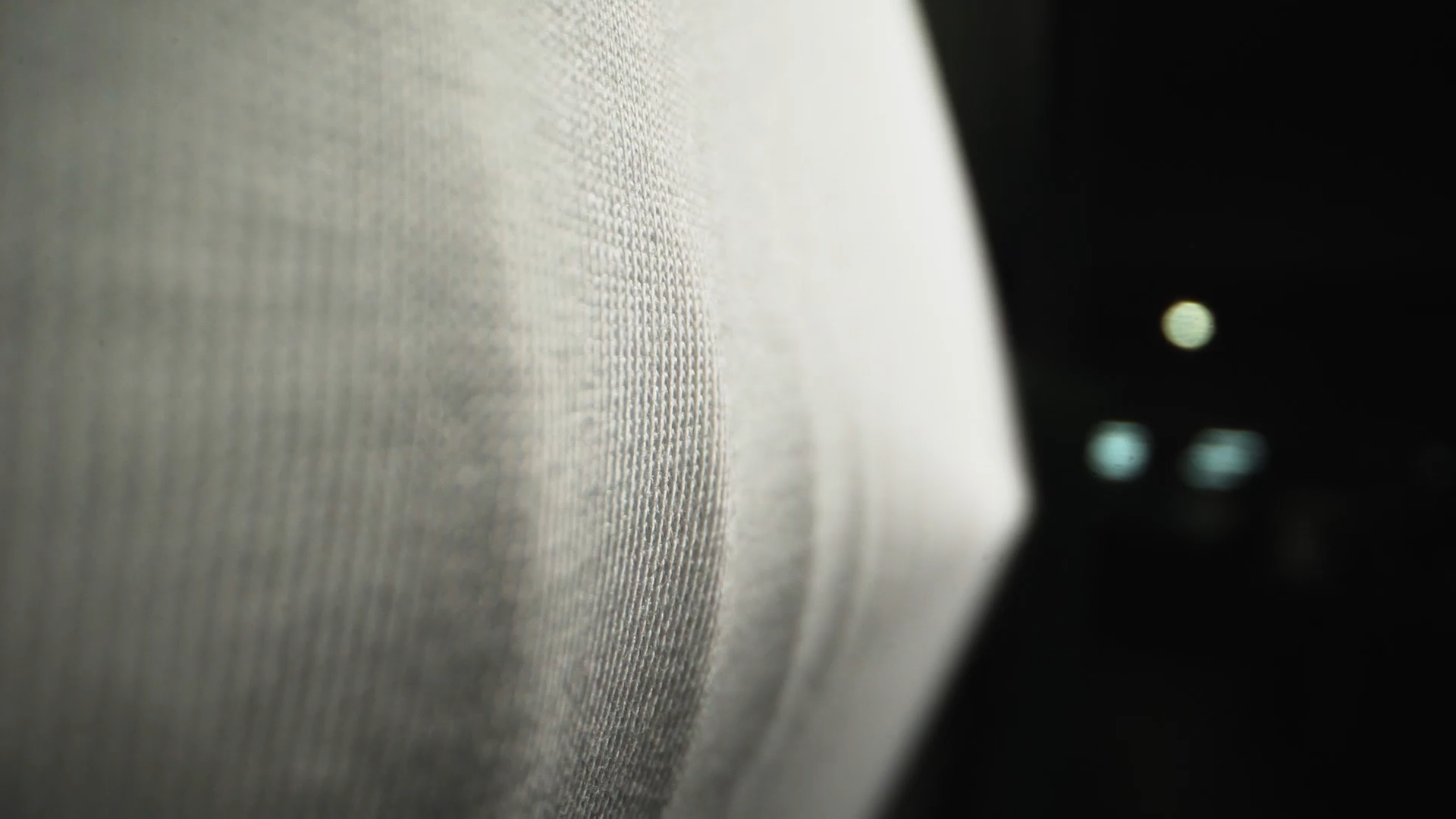
Jersey
Jersey is a knitting technique that is commonly used in clothing. It is easy to tell the difference between the front and back of a knit. The front has loops whilst the back has a flat surface. It is generally known for its flexibility and softness.

Fleece
Fleece Knit fabric is a knitted fabric that is brushed on one side, (usually the inside of a garment) and has a smooth, soft surface on the other side. It is a common fabric used for sweatshirts and hoodies. The result is an absorbent, heavyweight material that's super comfortable to wear.
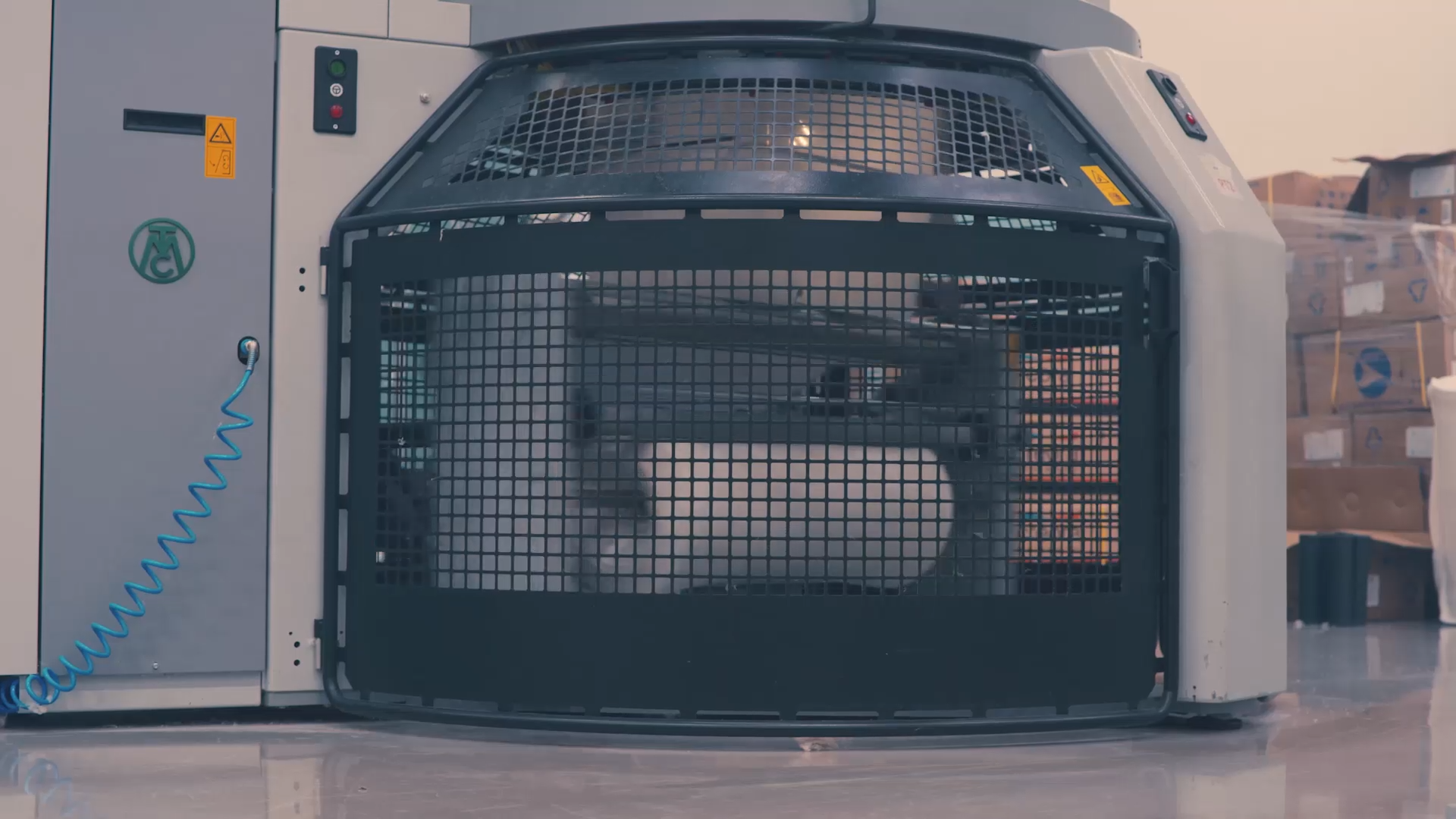
Circular Knitting
In circular-bed knitting machines, needles are implanted on a circular cylinder, which creates a seamless tube of fabric by joining the stitches from the needles. They exist in different sizes or diameters, depending on the field of application.

Yarn Count
Yarns that are produced for knitting are typically labelled with two numbers in what is often referred to as the ‘yarn count’. For example, on your index™ care label you may recognize the numbers 12/1, 20/1, 24/1, or 24/2. The second number indicates the number of plies of the yarn; a single yarn is designated with a 1, a two-ply yarn with a 2. The first number indicates the size of the singles in the yarn - regardless of fabric type, size 1 is the thickest and the higher the count, the thinner the yarn. Furthermore, the greater the number of plies, the thicker the yarn.